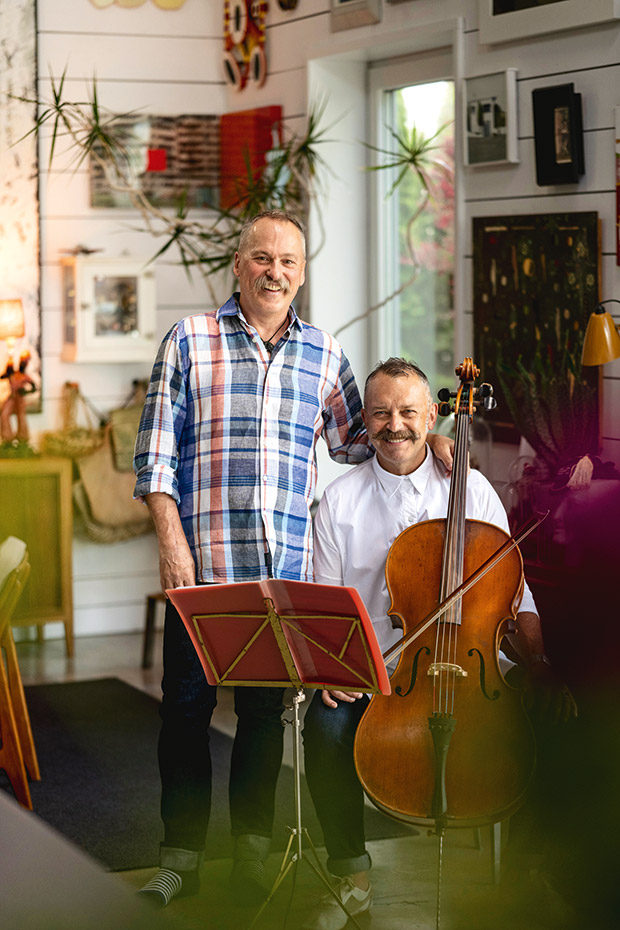
The eight-year-old Carterton home of Gregg Crimp (now a registered architect) and his partner David Robinson (also a graduate of the Victoria University School of Architecture) is a display case for repurposing.
A house so leak-free it might pop if air were pumped into it delights its owners-designers, who smile every day at its light and effective footprint.
Words: Kate Coughlan Photos: Esther Bunning
A pile of metal trays once used to steam vegetables for Wellington Hospital patients, discarded long ago during a hospital upgrade, would be both unremarkable and undesirable to most. But not to this pair of magpies, eyes honed by decades of junkyard adventuring. David Robinson and Gregg Crimp fell upon the trays, turning them this way and that and nodding excitedly to each other. They didn’t know what need the old trays might fill in the future — just that they would.
Into storage went the steamer trays. They joined a 100-year-old wooden staircase liberated from a junkyard in Eketāhuna and filing cabinets from the old Masterton Town Hall (reputed to have held the Treaty of Waitangi for safekeeping from war-time bombing threats). Also repurposed were rusty industrial steel shelves and items too numerous to list but carefully collated for future use.
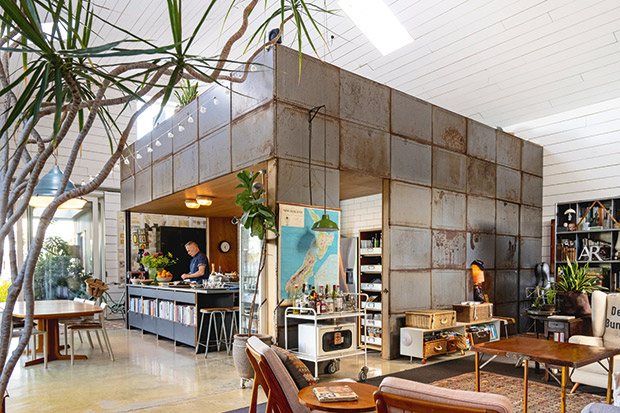
The relaxed industrial-chic interior of this 185-square-metre home belies the exacting scrutiny that went into getting it 100 per cent air- and weather-tight as well as aesthetically pleasing. Having done so, David and Gregg outfitted it with at least 75 per cent recycled or repurposed objects, such as formerly discarded rusty steel plates (once metal shelving) found in a junkyard near Upper Hutt. The plates, costing $1 each, now define the central area of the kitchen on the ground floor and the mezzanine office on the first.
Today, the eight-year-old Carterton home of Gregg (now a registered architect) and his partner David (also a graduate of the Victoria University School of Architecture) is a display case for repurposing. The steamer trays have been transformed into pull-out shelving in a pantry, and the staircase links the ground floor with a mezzanine-level office. The steel shelves, now cladding, define the central area of the house, and the filing cabinets (today te tiriti-free) are laden with jars of preserved lemons and homegrown preserves.
It’s the house of 100 stories, or possibly even 1000 stories, as every décor item and 75 per cent of its structure has had another life somewhere else. And that’s not the half of it. The other and perhaps even more significant aspect of this house (and why it won the NZIA Wellington Architecture award in 2020) is how it is built and on such a budget.
“Our last house was a Melrose mid-century-modern overlooking Lyall Bay and Cook Strait and no matter how much we renovated and insulated, it was a 1950s house. Single-glazed floor-to-ceiling corner windows; great views but cold.”
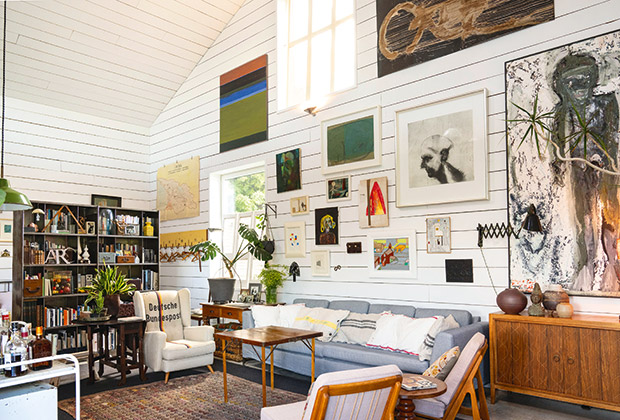
The sitting room is easily cleared out when Gregg and his fellow quintet cellists get together to play. He learned the cello as a pupil at Rathkeale College, then abandoned it to a cupboard for 35 years before taking it up again just over a decade ago. The rich Carterton music community provides unexpected joy.
Both men are provenly capable of starting again. After a successful career as a physiotherapist (specializing in sports medicine in Britain), Rangitīkei-born Gregg returned to Wellington and completed an architecture degree. Vancouver Island-born David, who gleefully and accurately ticks “Other Pacific Islander” on official forms (and is amused by the resulting invites to colourful Pasifika events), first came to New Zealand as a Rotary Exchange student in the 1980s and loved it. A career as a salmon fisherman and United Nations fisheries observer aboard driftnet fishing trawlers didn’t satisfy his creative leanings so, he too, enrolled in architecture school — but in Canada.
On a brief return to his Rotary haunts, he visited the Victoria University architecture school, was enthralled by the thought of continuing his architecture studies there, met Gregg and returned to Canada. And that might have been that except some things are meant to be. Gregg’s mother asked how he was getting on with that “nice young man from the west of Canada”, and Gregg replied that they were pen pals. She opened her Bank of New South Wales chequebook and said: “I think you should go and check in person.” He did, and David’s easiest-ever life decision was to accompany Gregg back home to New Zealand.
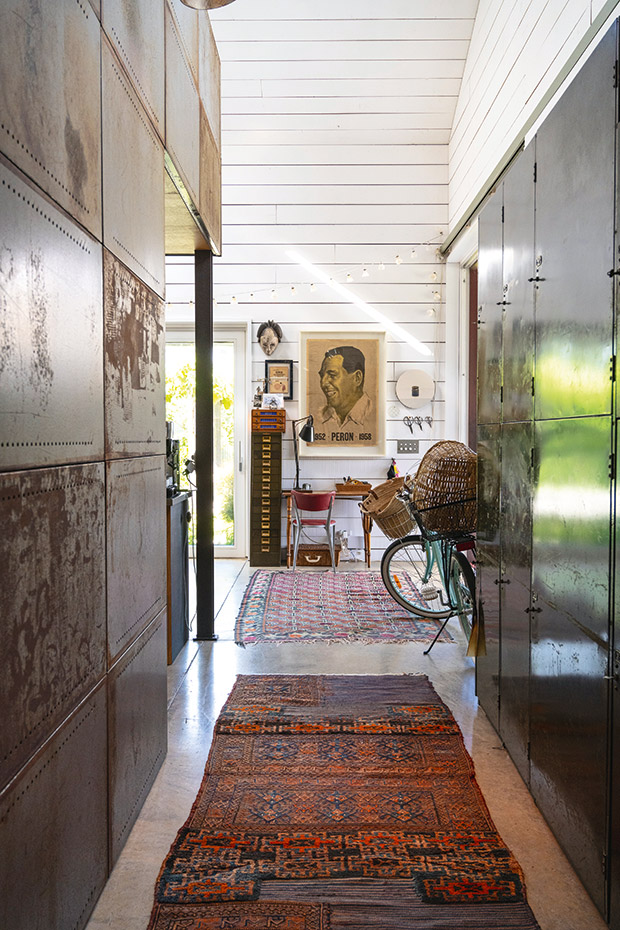
A Schwinn Sprite bicycle found at the local hospice shop makes for quick trips to town. David and Gregg are so close to the Carterton shopping hub that their days are punctuated by the chiming main street clock tower. Storage cupboards from the old Masterton Town Hall, reputedly used to protect the Treaty of Waitangi from wartime bombing threats, today store preserved lemons and pickled figs.
The decision to leave Melrose was also easily made, if not easily executed. The plan was to stay close to Wellington and their existing client base. The search zone reached as far north as Foxton on the west coast and Eketāhuna on the east.
Lifestyle blocks didn’t appeal — all that lawn mowing and driving to town for a bottle of milk. The goal was to renovate a house to their aesthetic requirements, within their finite mortgage-free budget and acceptable to their eco-friendly sensibilities. Simple, huh? Not until Gregg suggested they hit the “commercial property” button in their real estate search did they strike gold.
The automotive workshop, in an industrial cul de sac one street back from Carterton’s main road, was clearly unprepossessing as it had been on the market for some time. David and Gregg got very excited — the kind of feeling they get when they find a pile of steamer trays in a junkyard but much, much more powerful. The workshop was perfectly sited for sun, there was plenty of room to develop a garden on the northern side, and they loved the walking proximity to shops and cafés. The cul de sac spelt heavenly peace, and the building had an unprepossessing appearance — “low key” is an understatement.
They sold in Melrose, rented a house in Carterton, and began researching converting the rundown mechanics shed into an industrial-chic home. A party in the shed caused 120 of their Wellington friends to cry in unified horror: “What have you done?” The pig-on-a-spit roasting in the weed-infested, oil-drum-strewn backyard was, to be fair to their friends, the prettiest sight on offer. And that was just the exterior — things went from bad to worse inside the near-derelict building.
Soon, even optimistic Gregg and David had cause to pause. The dream of converting the shed loomed costly, time-consuming and challenging. “This building is poked,” said one contractor. “You guys are nuts,” said another. “Knock it down and start again,” a third agreed.
“We took a deep breath and gave ourselves the advice we often have to give our clients: ‘Don’t throw good money after bad.’”
Back to the drawing board to design a new build for the old footprint. A year of intense research into world-best practice showed very little employed in New Zealand. “It is very, very disappointing that so many New Zealanders must suffer the consequences of living in cold, drafty homes.
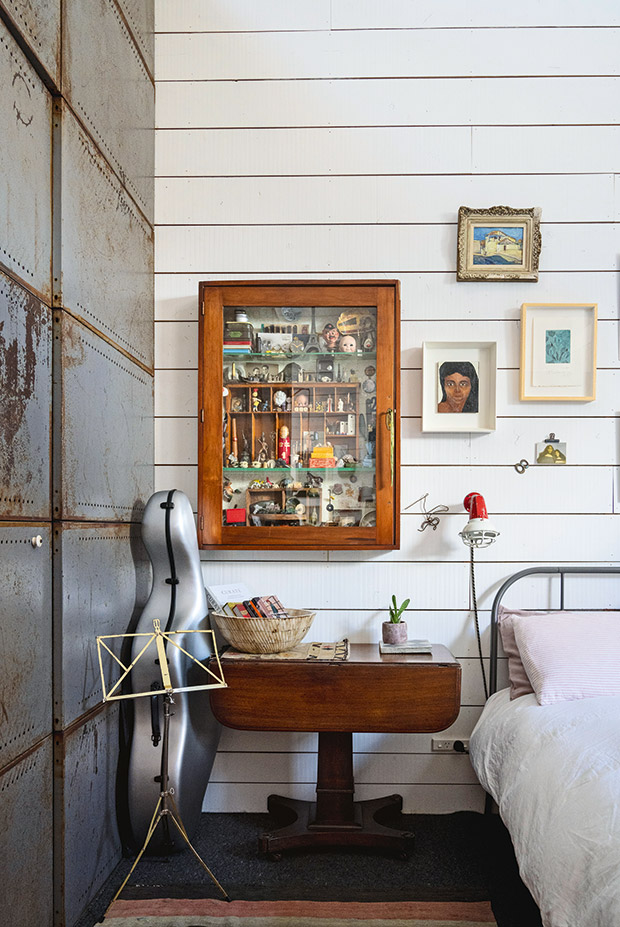
“Our guest bedroom (opposite) is tucked behind the large bookshelf in the main room with secret-door access to their bathroom. Guests say they love sleeping here and don’t feel the need to be walled off into their own sleeping space.” The “cabinet of curiosities” is a shrine to found objects.
“Wooden tents,” says David quoting a European friend who was shocked at the poor quality of New Zealand housing and what New Zealanders are prepared to put up with in their homes. What they learned about creating an efficient home comes down to three physical principles: radiation, convection and conduction. And not one element can be implemented or addressed in isolation.
“Despite a misapprehension that we live in a sub-tropical paradise, New Zealand’s climate is very challenging for two reasons — high humidity and a huge daily temperature change. Add to that the misguided notion that just by adding insulation into houses, cold and damp are prevented — nonsense.
“Most Kiwis — including, it seems, the government — have been sold into believing this concept, but the laws of thermodynamics mean that without addressing the three means of heat transfer [radiation, convection and conduction], best building performance for reduced energy inputs and optimum levels of human comfort cannot be achieved.
“Take one square metre of wall and insulate it; if there is even a one-millimetre gap around the insulation, its R-value — or measure of resistance to heat flow — is cut by about 50 per cent.”
Additionally, their industry experience has shown that many of the insulation systems used in New Zealand homes seldom work efficiently in the long haul because of inherent material properties and poor or incomplete installation.
“We see this all the time when we do renovations: we take off the wall linings, and all the lovely insulation is compressed and slumped inside the wall. Useless. Not insulating anything. It doesn’t hold its loft if there is a free flow of moisture and air through the wall.”
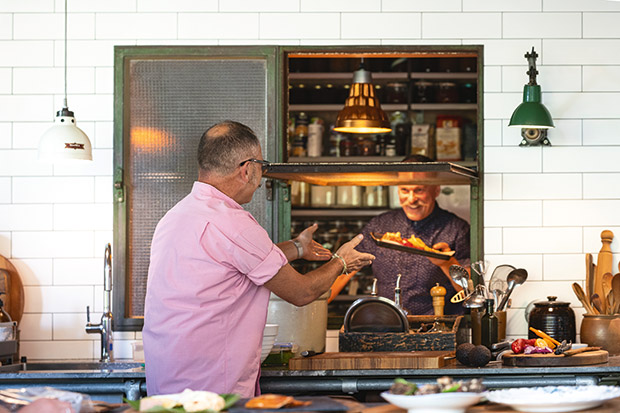
The kitchen, which includes a large scullery (or butler’s pantry) accessed through the lifting hatch, cost less than $5000 and is built mainly from repurposed materials, including retired scaffold pipes, plus truck-deck ply (cheap as chips but very hardy) and a zinc benchtop. The white tiles were purchased at an end-of-line sale from a shop in Petone.
And why does moisture come through the wall? “The daily temperature variation in most of this country is massive. In winter, here in Carterton, for example, it might be minus five degrees Celsius overnight and go above 18 degrees Celsius outside during the day.”
“That’s a 23-degree shift in temperature. Typically, a ‘modern’ house has been constructed with walls comprised of 90 millimetres of stud, 10 to 12 millimetres of Gib inside and 22 to 25 millimetres of exterior cladding. So that’s all trying to hold back the loss of 18 degrees of temperature, and somewhere in the middle of the wall, the temperature will hit the magic number of 12 degrees at which moisture condensates. Where does it condensate but inside the wall assembly?
“New Zealand’s very high humidity conditions must be accommodated in planning and building for energy efficiency. Most Wellingtonians, for example, would not realize that the average humidity in that city is 70 per cent.”
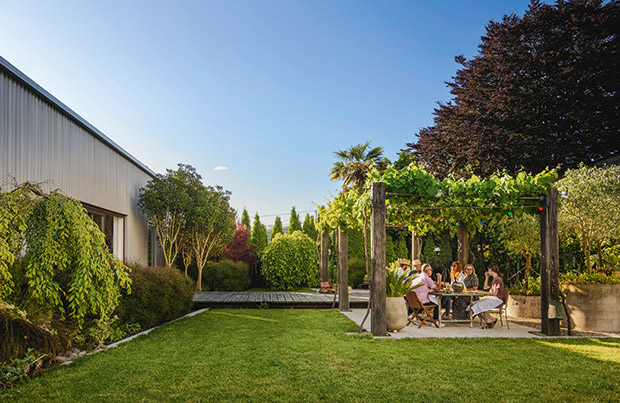
Fig trees espaliered along the boundary fence are prolific fruiters, as are the table grape vines thatform a leafy shelter from the harsh Wairarapa sun. It’s hard to imagine the space was once covered in blackberry bushes, strewn with oil drums and discarded steel objects.
The No.1 bit of advice from David and Gregg’s research and experience is to spend money on a building’s envelope; seal the shell encompassing the entire structure. “Don’t go airfreighting in a Viking oven from the United States — please no. The money must go on an airtight envelope first.
“Our building process came at the right time for us as we’d been collecting and working in the field for several decades when we set out to put it into practice. So, we say these things with experience.
“Every day we wake up, and we count ourselves lucky and realize how privileged we are. Yes, it is our hard work, but we have had great good fortune and luck along the way. We remind ourselves that New Zealanders are doing it tough out there without the same choices and opportunities we’ve had. So, we never take it for granted — our community and culture, a little bit of land to grow things and sharing our knowledge and learnings with our local community.”
HOW THE HOUSE IS CONSTRUCTED
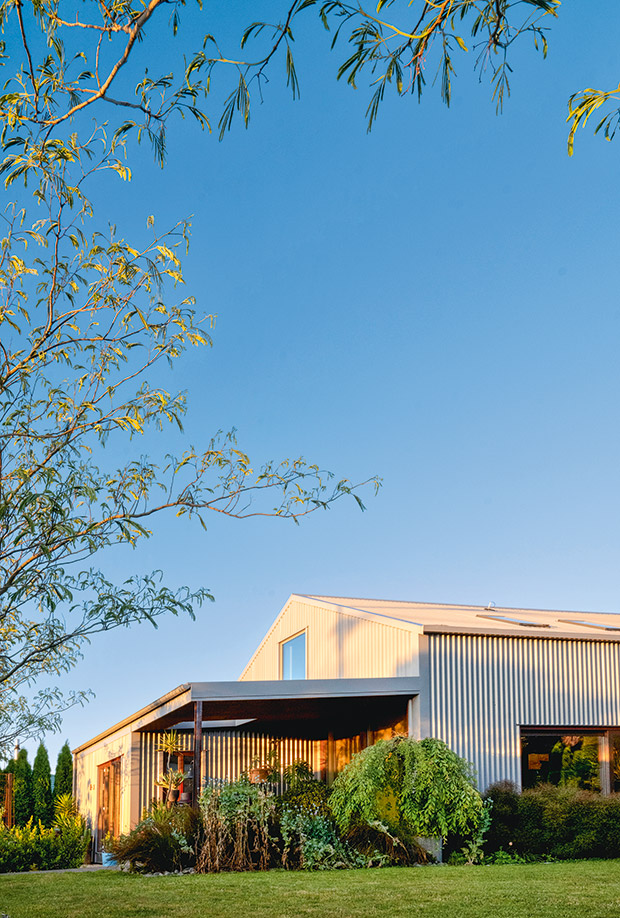
Even though the house is on a quiet cul de sac in a semi-industrial part of Carterton, passersby often wander right up the front path and peer in the huge sliding glass door. The one-way glass means they have no idea the occupants are watching them.
Foundations: 120-millimetre steel-fibre reinforced concrete Ready Floor slab, using part of the original footprint plus footings to support three portal frames. Isolated from thermal bridging with 50 millimetres of rigid foam insulation.
Advantages: Reused part of the original foundations, cut back to nib walls and not radiating any heat back into the ground below. The Eketāhuna Earthquake of 2014 proved floor-slab performance within four days, leaving only a superficial crack, even though the concrete had not cured.
Frame: Light gauge, mild galvanized steel girts and portal frames prefabricated by Coresteel Buildings, Whangārei, delivered stacked on a truck. It was the first domestic building using this commercial/industrial system, and it offered a wide span without the requirements of internal groins and visible cross braces.
Advantages: Delivered on-site 100 per cent-ready for erection; less scaffolding, minimal labour cost, zero waste.
Seal: Two layers of Pro Clima building wrap, one watertight on the outside (Solitex Extasana) and a vapour-diffuse airtight membrane on the inside (Intello).
Advantages: A high-performance German system of sealing for weather tightness and airtight construction, easily taped to achieve a blower-door-tested result of 1.0 ACH (air change per hour). “Like a Gore-Tex jacket in which moisture permeates out.”
Insulation: Polyester blankets and pads by Mammoth are 100 per cent polyester, manufactured in New Zealand from 60 per cent recycled plastic bottles.
Advantages: Stiff pads and high loft blankets with thermal and acoustic insulation are easy to cut; no health risks in installation; recycles plastic bottles, and every offcut is recyclable.
Exterior cladding: ColorSteel trapezoidal profile for both roof and walls.
Advantages: Money saved on the roof and exterior painting; the finish was a welcome nod to the semi-industrial history of the site.
Windows: Triple-glazed, imported from Germany at 25 per cent more cost on-site than locally made-double glazed windows.
Advantages: The glass sliding doors’ large span wasn’t available in locally made products without horizontal stablizing bars and smaller pane sizes. The extra cost, amortized over seven years, is $1409 per year for lifetime superior internal comfort and energy savings.
Interior finishing: Rough-sawn nine-year seasoned, untreated macrocarpa, face and edges finished with Natural Paint Company paint — zero-volatile organic compound paint.
Advantages: Able to use a stack of macrocarpa found at a local sawmill originally destined for pallet construction; a lovely timber smell of macrocarpa; cost-effective.
Steel panels reused from shelves salvaged from the rear yard of a building demolition/salvage yard in Upper Hutt. Cost: $1 per panel.
Advantages: Delineates an area of the structure and honours the site’s original semi-industrial history. Cheap.
Unintended advantage: Perfect acoustics make the space pleasing for an amateur cellist and for attendees at cello and other musical concerts hosted at home.
STAYING WARM
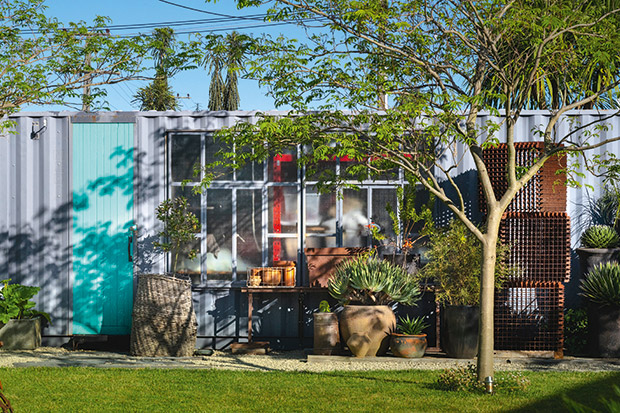
The 12-metre steel container was placed two metres back from the road so a ribbon of green beauty could face the street. Old windows from the Hope Gibbons Building in Wellington’s Tory Street were welded into the container to provide an attractive façade and allow in light.
“We didn’t want to be running six heat pumps or stoking roaring fires and chopping kindling. So, there’s no open fire and only a two-kilowatt heating panel that is turned on for a few days each year in mid-July — if there is no sun for a few days. The concrete floor soaks up the sun even in winter and releases it as the temperature drops. The house is pretty much constantly at 20 degrees Celsius in summer and winter. We think we are freezing if the inside temperature drops to 17 or 18.”
Power bill: For a house of 185 square metres, with four computers, two fridges and two full-time “profligate users of electricity”, the annualized kilowatt-hour since 2015 is 9125 a year, costing between $200 and $300 a month. “The thermal performance of the build is working extremely well for us as a passive house with as little input as possible for human comfort.”
Cost: “Stage one, including the foundations and the enclosed 110-square-metre shell (frame, roof, windows, sealing wraps and insulation), cost $105,000. The main building is 12 metres by nine metres witha 30-square-metre mezzanine and a further 35 square metres for our bedroom and bathro ing. “Per square metre, the building cost was $1800 when most buildings cost $4000 per square metre.”
MORE HERE
From junk to treasure: Foxton’s DIY queen Mel Cowan turns heads with her elegant upcycled creations
Waitākere artist Mandy Patmore paints a brighter future for young creatives
Take a tour of fabric upcycler Sarah Lancaster’s cute-as-a-button tiny house
Love this story? Subscribe now!
The post Grand designs on a budget: A clever couple turns junk into a curated Carterton home appeared first on thisNZlife.